Analysis
Project Requirements
-
Can be operated by one person.
-
Must be able to produce 25 acceptable parts in succession without failing.
-
Flash can be no longer than 0.010”.
-
Insert must fit with a tolerance of 0.002”.
-
Project cost cannot exceed $1000.
-
Cannot exceed 50lbs.
-
Moving parts cannot jam or bind during operation.
Sketches of ideas

An idea to have the cavity section of the mold separate and replaceable. That way, instead of designing and constructing an entirely new mold one could merely design a new cavity insert that could be swapped out.

The Ejector Plates in the mold are held in place by four springs. In order to know which springs to buy we needed to calculate the minimum spring rate that is needed to keep the Ejector Plates in place. The spring rate for the springs was found to be .042 lb/in.
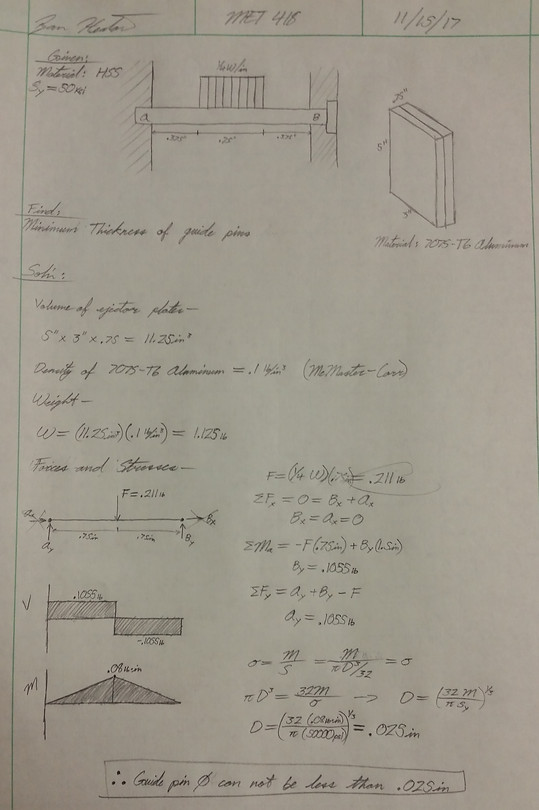
The Ejector Plates are riding on four guide pins. Since we don't want the pins to break of deflect in any way we had to calculate the minimum diameter that would support the weight of the Plates. the minimum diameter came out to be .025in.

The thermal expansion of the aluminum needed to be known so we can make sure that nothing breaks or binds. The 3.5" piece of aluminum was found to expand by about .0165". But this is at a temperature of 430 degrees F which was the melting temp for the chosen plastic material at the time.
During testing the mold never got hotter than 125 degrees F. If the calculations were done over with this temperature the expansion would be about .00289".

The thermal expansion for the plastic material was needed so the cavity can be scaled to make up for the shrinkage that occurs during cooling. The scaling factor was found to be 1.018.

The total weight of the mold was needed because one of the requirements for this project is that the mold must weigh less than 50lb. the mold design should come out to be only about 9.46lb.