Construction
The mold will be made up of 4 main Plates, 2 inserts, and 2 ejector plates. Each main section will be milled from 7075-T6 Aluminum Stock. The cavity for this mold will be milled into inserts, a separate piece that will be interchangeable within Plates A and B (see Appendix B). That way multiple inserts can be exchanged to produce a new part instead of replacing the mold entirely. Other smaller pieces like the Sprew and Ejector knob will be made on a lathe and or manual milling machine.


All of the plates and inserts were rough cut from 7075-T6 aluminum bar stock. It was decided that it would be more efficient to work on all of the parts at the same time than only doing one part at a time. That way, if mistakes were made, they would be found immediately.

Each part had to be CNC machined in order to maintain a tight tolerance. the tight tolerance was needed because the mold has to fit together perfectly in order to not produce any flash. (flash is when the molten plastic spills out the side of a mold)

Each guide and ejector pin had to be individually cut and ground to size. If the length is off on any of them it could result in a faulty part.
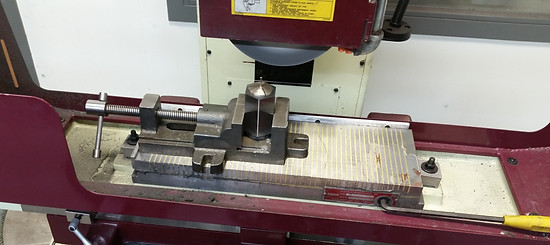
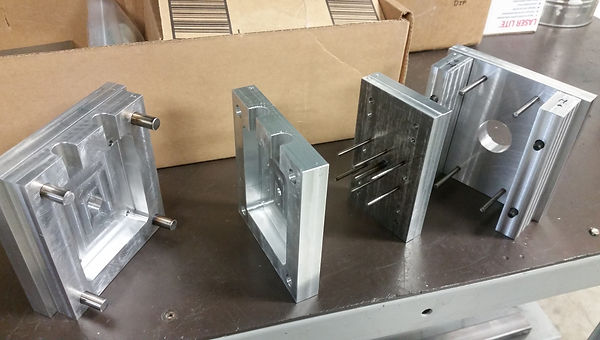
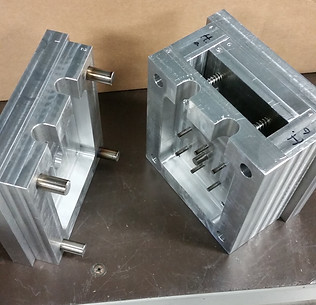
Fitment is very important for any kind of die casting process. Fitment tests were regularly conducted in order to make sure no mistakes were being made.

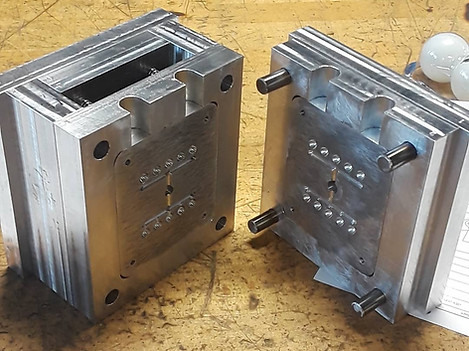