Testing

Mold in the Morgan Press.
In order to test the mold itself it will be mounted into the Morgan plastic injection press and the press filled with plastic material. The press will melt the plastic and inject it into the mold. The mold will then be removed from the press and opened, split between Plates A and B, and eject the part by pushing the ejector plates/pins forward. If the mold is working properly and the settings are correct, there will be no flash or defects in the part produced and the mechanical parts of the mold won’t jam or bind. There also will not be any problems with plastic sticking to the inside of the mold and getting stuck. If that happens the mold will have failed to eject the part properly.

Part in the mold before ejection.
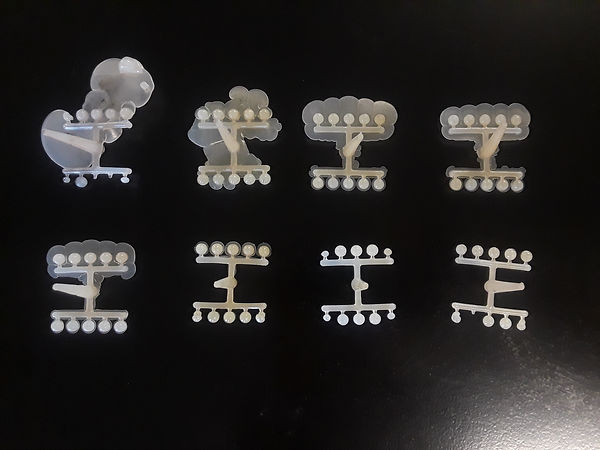
The optimal heat and pressure settings for the press and mold had to be determined in order to produce successful parts. Because the material properties for our material were unknown, many test runs had to be done at different settings to find what worked best. About 60 faulty parts were made before the optimal settings were found. A faulty part would be a part with voids or flash.
Once the optimal settings were found the production runs could start. The requirement for this project is 25 successful parts in succession. The mold made 37 acceptable parts in succession. It could have been more but the level of material was not being monitored well enough. The faulty parts were due to running out of material not the mold.
Faulty parts. Plastic overflow (flash) and voids.